СТРОИМ АСТАНУ ВМЕСТЕ
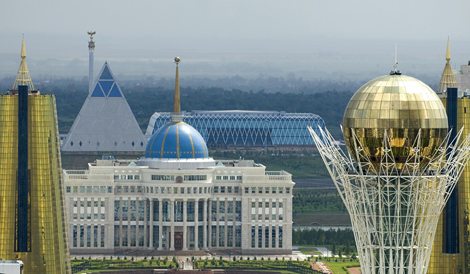
Более 20 восточноказахстанских предприятий стройиндустрии поставляют сегодня свою продукцию на строительные площадки столицы.
Традиционным лидером является Бухтарминская цементная компания, которая за пять месяцев 2016 года поставила в Астану 118 тысяч тонн высококачественного цемента различных марок.
Более 60 тысяч тонн закупил с начала года крупнейший производитель товарного бетона Казахстана – товарищество «Астанастройконструкция», которое поставляет изделия на многие строительные площадки молодой и активно строящейся столицы. С помощью цемента Востока возведен целый ряд знаковых скульптурных комплексов, новых культурных, спортивных объектов нашей красавицы – Астаны. Всего в нынешнем году на стройки Астаны планируется отправить с бухтарминского завода около 300 тысяч тонн цемента.
Разумеется, только безупречное качество может служить гарантией пропуска на столичную стройплощадку. Та же Астанастройконструкция испытала продукцию многих цемзаводов. Остановились столичные производители бетона на бухтарминской «пятисотке». Но доверяют, да тщательно проверяют. Так что укрепляют всеми силами наши цементники давнюю традицию завода – качество прежде всего.
К тому же бухтарминцы свое-
временно разработали марки цемента для условий агрессивных сред. Гармонизировали стандарты с тем, чтобы они соответствовали мировым. Это оценили иностранные инвесторы, работающие, в частности, по европейским стандартам. Разрабатываются и новые виды цемента: морозостойкий, пластифицированный, которые можно использовать при низких температурах. Вместе с высоким уровнем сервиса, стабильностью поставок это имеет важное значение.
Весь комплекс работ проходит под строгим контролем заводской лаборатории. Недаром на заводе любят говорить: без лаборатории нет цемента. Здесь проводится большое количество всевозможных замеров, анализов, испытаний – сырья, топлива, полуфабрикатов, конечной продукции. Ведь цемент, обернувшийся в бетон и строительный раствор, должен служить вечно.
Лаборант отдела физико-механических испытаний формирует лепешки из цементного теста. Затем приборами замеряется густота, расплыв материала, время начала и завершения схватывания. Такие лепешки три часа кипятятся в воде.
И если в цементе будет, скажем, перебор по свободному оксиду кальция, то лепешка увеличится в объеме. Вообще же, цемент набирает марочную прочность в естественных условиях через 28 суток. Тогда «спрос» с него полный. Инженер физико-механических испытаний демонстрирует: балочка «возрастом» 28 суток должна выдержать при сжатии давление не менее 400 килограммов на квадратный сантиметр, при изгибе 55-60. Бухтарминский цемент экзамен держит! Поэтому этот вид цемента называется маркой 400. А тот, который держит давление в 500 килограммов, носит еще более гордое имя марка 500.
Забота о качестве начинается на заводе со входного контроля. Лаборант по входному контролю сырья, топлива при помощи весового, химического и других методов определяет качественный состав основных сырьевых составляющих – известняка, глины, железного огарка. Сегодня содержание карбоната кальция в известняке может быть одно, а завтра другое. Также, как и в глине оксидов кремния, алюминия и так далее. Столь же важен и химический состав огарка. Качественное состояние сырья определяет пропорции рабочей смеси – шлама. За соблюдением пропорций на местах строго следят лаборанты цехов. Вот и сейчас контрольный мастер смены делает очередной отбор шлама. Необходимые корректировки по компонентам выполняет машинист шламнасосов. И снова машина, ходящая по диаметру большого бассейна доводит шлам до состояния однородной массы. Сегодня в ней процентов 75 известняка, 20 – глины, 2,5 – огарка.
Специальные питатели подают шлам в большую вращающуюся печь, в которой он спекается в клинкер. Заглядываем в смотровые окна. Там внутри ревет пламя, перекатывается спекающаяся масса. 62 тонны клинкера в час дает эта печь. Сегодня здесь работают «пятисотку», то есть выпекают клинкер на марку 500. Температура в зоне горения достигает 1700 градусов, а спекание происходит при температуре 1400.
Глядя на мониторы компьютера, машинист вращающейся печи весь производственный цикл видит как на ладони. Процесс управления технологическими процессами последовательно автоматизируется в соответствии с лучшими мировыми образцами. Да, клинкер – ключевое слово цементного производства. Обжечь хороший клинкер, значит получить хороший цемент.
И едва он остывает, за дело снова берется лаборатория. Инженер-аналитик измельчает гранулы клинкера до тонины сита 0,08 и при помощи приборов определяет его качественный состав. Удалось ли получить нужные параметры? Тщательная работа с сырьем дает свои плоды. Но и клинкер нужно правильно размолоть, как здесь говорят.
Внушительно рокочут могучие цементные мельницы. В зависимости от задач на этом этапе в цемент добавляются различные дозировки гипса, граншлака, известняка, а теперь и других минеральных добавок. А пробы отбираются через каждый час работы мельниц, которые затем подвергаются испытаниям.
И чтобы уж совсем быть уверенным в качестве своей продукции, физико-механическим испытаниям подвергается каждая подготовленная к продаже партия и окончательный контроль отбора проб цемента из каждого вагона.
Мы гордимся тем, что нашу продукцию ждут стройки столицы.